汽车
如果您正在寻找提高可回收性或减少碳足迹的方法, Kraton 可提供解决方案,并综合提高性能。 从汽车内饰的仪表板和门板蒙皮,到外饰的保护膜和涂料,我们的产品提供多样化的性能表现,帮助提升车辆驾驶体验,降低碳足迹。
汽车
热塑性弹性体 汽车行业
文献
优势
核心价值观
IMSS技术
Kraton IMSS™技术是一项革命性的技术,通过最新一代的热塑性弹性体(TPE)聚合物技术实现表皮的注塑加工,达到柔软触感和减重效果。 IMSS实现了大面积薄壁注塑薄壁软皮部件(如薄至1 mm的仪表板蒙皮)提高了制造效率。 可使用普通的注塑机和加工条件,包括 单色 和 双色 工艺。 与现有的PVC搪塑表皮相比,该产品可以减重25%,并可以无需修改的直接复制现有搪塑表皮的A面设计。 IMSS助力各种对环境负责的举措,包括车辆轻量化,和生产报废品和生产边角料的回收利用。
应用
- 内饰仪表板
- 内饰门板
- 中控包覆件
主要优势
- 节省系统成本
- 可实现大面积薄壁零件的注塑成型
- 减轻车辆重量
- 改善耐老化性能
- 改善车内空气质量
- 提升感官品质
- 实现软皮的可回收
搪塑软皮
Kraton 搪塑术为制造商提供了一种轻质、环保、可持续的解决方案,并改善了制品的耐老化性能。 我们的热塑性弹性体 (TPE) 技术比现有产品性能更优,并能够利用当前的加工设备生产触感柔软的内饰部件。
新一代搪塑产品具有关键优势,包括低密度特性,满足 OEM 轻量化需求;无需额外设备,适用于现有搪塑设备;以及优秀的长期耐老化性能,如助力安全气囊在车辆全使用周期内的可安全展开。
TPE 搪塑软皮技术能实现汽车内饰设计的所需功能。 这为零部件制造商和汽车主机厂提供了更大的设计灵活度,用于生产各种汽车内饰部件。
应用
- 内饰仪表板
- 内饰门板
- 包覆件
功能
- 密度更低
- 无需交联,不含邻苯二甲酸酯,增塑剂含量低
- 优异的耐磨性/耐久性
- 低温柔韧性
- 实现柔软触感
- 可搪塑工艺的设计灵活度
- 可使用现有的搪塑和发泡方案
- 材料的自然本色清透
主要优势
- 减轻车辆重量
- 改善耐老化、低雾化、低VOC、低气味
- 符合 OEM 性能规范
- 低温柔韧性
- 提升感官品质
- 可实现小角度和严重倒扣的软皮设计
- 无需额外的资本投资
- 出色的着色性
可回收设计
了解 Kraton 聚合物如何帮助品牌在产品设计中最大限度地利用回收成分。
汽车应用
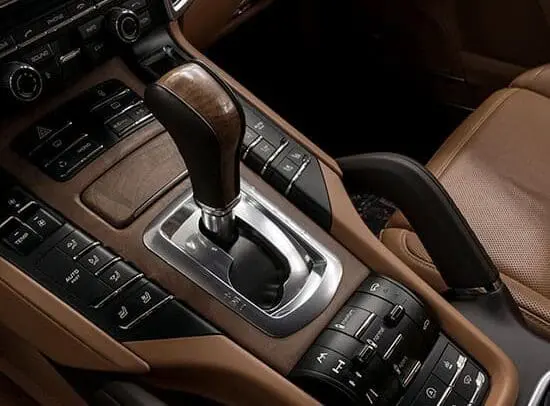
仪表板软皮
Kraton IMSS™技术是一项革命性的技术,通过最新一代的热塑性弹性体(TPE)聚合物技术实现表皮的注塑加工,达到柔软触感和减重效果。
触感柔软的内饰件
基于 Kraton HSBC的热塑性弹性体(TPE)因其柔软的触感和出色的配色性能而广泛用于汽车内饰。 应用包括控制台垫、杯架衬垫、旋钮包胶、把手和挡板。 也可以制成适合不同基材的包胶材料,从而最大限度地减少额外的组装步骤。
加工工艺
- 共混改性
- 注塑
技术/产品
- Kraton™ G1650 , Kraton™ G1651, Kraton™ G1654
- Kraton™ G1640 , Kraton™ G1641, Kraton™ G1642
- Kraton™ FG1901
- Kraton™ MD1648
- Kraton™ MD6951
功能
- 马来酸酐官能团
- 更高的流动性
- 易于配方设计
- 稳定的SEBS主链结构
- 高质量、稳定的产品性能
- 高氢化水平
优势
- 具有出色的极性塑料附着力
- 减少最终产品的质量缺陷
- 更高效的共混改性
- 柔软的触感
- 在共混中更有效地混合各类不相容材料
- 良好的耐紫外线性能
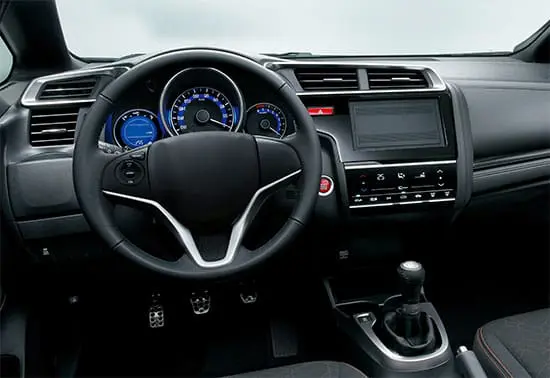
方向盘安全气囊盖
安全气囊的一个关键安全性能是气囊可从盖体下方顺利展开。 并且还要求气囊展开时盖体不能出现脆性破裂,导致盖体碎片高速飞出。 在低温下传统工程塑料会变得更脆和更硬,因此存在此高风险。 Kraton 聚合物为安全气囊盖提供了更好的低温柔韧性。
因安全气囊盖为非常显眼易见,改善其外观同样至关重要,如颜色均一和无注塑缺陷。 耐刮擦性也十分必要,因为驾驶员会频繁触碰到安全气囊盖。 Kraton 产品具有更高的流动性和出色的相容性,可增强着色性并降低出现如虎纹和凹痕等缺陷的风险。
加工工艺
- 共混改性
- 注塑
技术/产品
功能与优势
- 低温韧性
- 更高的流动性
- 更高的流动性
- 在共混改性中混色更高效
- 更高效的共混改性
地垫和地毯背衬
地垫和地毯背衬提供柔软的缓冲效果。 这些对成本敏感的应用通常使用更多的油和填料,以及回收料。 产品必须使用更好的相容剂,才能实现高充油比,同时不出现油析出问题。
Kraton 聚合物可用于替代地垫或地毯背衬中使用的橡胶或PVC。 我们的产品提供更有效的锁油能力,提供柔软的触感,避免油析出并降低成本。 聚合物还具有出色的相容性,可在共混时更有效地的分散相容异种材料,减少增塑剂迁移和橡胶气味。 注塑成型的地垫可实现定制化产品,更美观和更易清洁。
加工工艺
- 共混改性
- 挤出型材
- 注塑
技术/产品
功能与优势
- 高效吸油
- 更高的流动性
- 触感柔软,无油析出,成本更低
- 共混不同种类的材料更高效
- 无橡胶气味或无增塑剂迁移
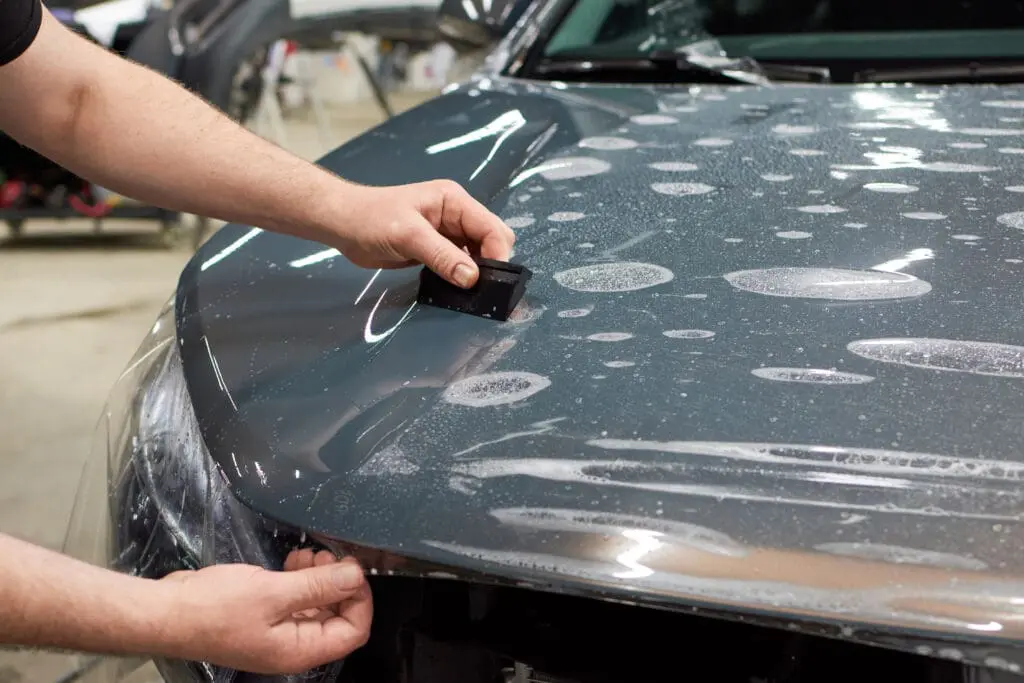
可剥离涂层
可靠的弹性可剥离保护涂层
用Kraton™ G SEBS聚合物制成的彩色透明弹性可剥离涂层可以粘附在喷漆的金属或塑料表面,防碎裂、划痕、水渍和腐蚀,提供可靠的保护。 当不再需要涂层或者想更新外观时,涂层能轻松剥离并且不会留下任何残留物。
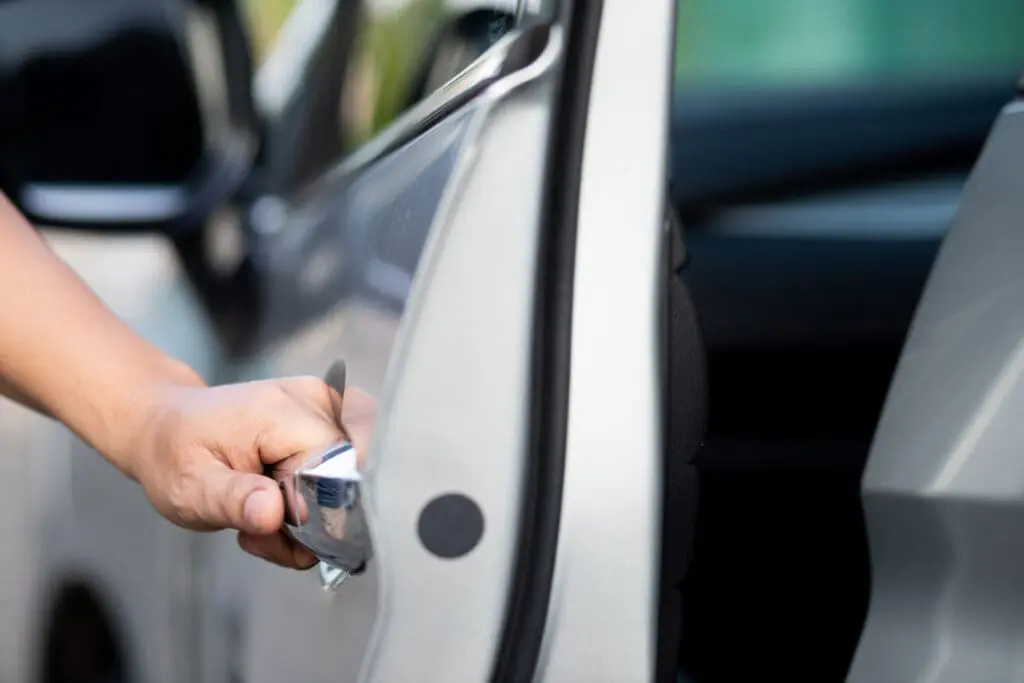
密封条、车身密封件
对于耐候密封和车身密封件来说,美观和良好的密封性能至关重要。 Kraton 产品能让产品颜色更均以稳定,耐候性更好,并且低压缩永久变形的特性,保证了良好的密封性能。 为了改善触感,我们有低硬度的聚合物,能使表面更柔软。
Kraton 高流动性的聚合物帮助材料降低成型压力,帮助包胶工艺更稳定,减少与接角注塑件的工艺缺陷,即使需要接角粘接非TPE材质,也能良好粘接。 在玻璃封装注塑中,较低的成型压力可减少玻璃破碎的发生。
由于具有出色的相容性和高流动性, Kraton 可以提高挤出型材的尺寸品质和生产线速度,而这些问题一直都是三元乙丙橡胶挤出的工艺难题。
我们的聚合物可帮助提升汽车密封件和密封系统的性能,提供超越现用材料的额外价值。
加工工艺
- 共混改性
- 挤出型材
- 注塑
技术/产品
- Kraton™ G1651
- Kraton™ G1651, Kraton™ G1633, Kraton™ FG1901, Kraton™ MD6684 (共挤/包胶成型的密封件)
- Kraton™ G1633 (耐候密封/车身密封件)
- Kraton™ G1633 (发泡密封件)
- Kraton™ G1651, Kraton™ G1641, Kraton™ MD6951, Kraton™ MD1648 (密封件)
功能
- 易于加工
- 低压缩永久变形
- 工艺周期短
- 可再加工和回收使用
- 低温韧性
优势
- 密封性能好
- 更高的流动性
- 减少最终产品的质量缺陷
- 减少玻璃的损坏
- 更高效的共混改性
- 提升接角注塑、刚性部件上的低硬度软皮包覆和密封系统粘接成型的粘接力